Before (改善前)
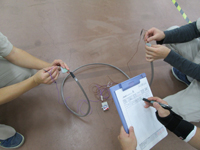
制御盤製作において、ケーブル製作・ケーブル実装後の導通検査は当然の事ですが、弊社では、以前から行っている検査方法で手動による導通検査をしています。
【メリット】
・単品ケーブルの検査に向いている。
・状態異常を確認しながら作業出来る。
・改造・改修作業等、手軽に行える。
【デメリット】
・作業工数がかかる。
・人員の増加。
・人為的ミスが出やすい。
【メリット】
・単品ケーブルの検査に向いている。
・状態異常を確認しながら作業出来る。
・改造・改修作業等、手軽に行える。
【デメリット】
・作業工数がかかる。
・人員の増加。
・人為的ミスが出やすい。
制御盤製作では、導通検査の際ブザーを使用して検査をしています。確認項目を読み手が一人で読んでチェック項目にチェックをしていき、当たり手二人でケーブルの端と端を持って導通・コネクタピン挿入位置・ラベル等の確認を行います。この方法はケーブル単体での検査には良いのですが、ケーブルを装置に実装後はケーブルの末端から末端のコネクタが遠くなります。また導通確認をする時の声が聞き取れないと言うヒューマンエラーを起こす可能性があります。
V
After (改善後)
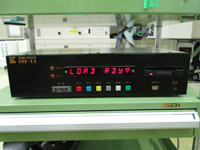
制御盤製作において、ケーブル実装後の検査は必須ですが、手動による検査では作業工数や人員の増加・人為的ミスが発生しやすくトラブルにつながります。よりトラブルを簡単に回避出来る検査機での検査が良いです。
【メリット】
・検査工数の削減。
・作業人員の削減。
・量産化に適している。
・人為的なミスを防げる。
【デメリット】
・専用治具を製作するための初期費用が必要。
・初号機からの対応が困難。
【メリット】
・検査工数の削減。
・作業人員の削減。
・量産化に適している。
・人為的なミスを防げる。
【デメリット】
・専用治具を製作するための初期費用が必要。
・初号機からの対応が困難。
検査機を使用する事により、検査工数を大幅に短縮出来る上に、ヒューマンエラーを防ぐ事が出来ます。量産タイプには検査機での検査が良いでしょう。また検査機を使用するためには、専用の検査治具を製作するためのコストがかかってしまいます。検査工数・作業人員が削減出来るため、装置が量産化になればなるほど総合的なコストの削減になります。